Отливка: путь от расплава к готовому изделию
Существует несколько основных видов отливки:
-
Полуфабрикаты: чушки, требующие переработки в дальнейшем.
-
Слитки: подвергаются обработке давлением.
-
Фасонные отливки: обрабатываются с помощью резания.
-
Готовые изделия: не требуют механической обработки, лишь очистку или декоративную покраску.
Для отливки используются разнообразные материалы: металлы и сплавы, стекло, пластмасса, воск и др. При этом около 80% заготовок получают методом литья в песчаные формы, но такие отливки требуют обязательной доработки перед отправкой заказчику.
Литейное производство позволяет получать заготовки высокой точности, даже с самой сложной конфигурацией. Технология изготовления зависит от размеров и требований к будущему изделию.
Существует три основных группы получения отливок:
-
В разовых формах: форма используется только для одной отливки.
-
По растворяемым моделям: модель изготавливается из растворимого материала (воск, парафин), который затем удаляется из формы перед заливкой металла.
-
В формах полупостоянного и комбинированного типа: формы изготавливаются из огнеупорных материалов и могут использоваться неоднократно.
Помимо этих основных видов, используются и комбинированные варианты литья.
Литье металлов: от расплава к заготовке
Литье металлов – это технологический процесс, при котором расплавленный металл заливается в литейную форму, где он остывает и затвердевает, принимая ее форму. Форма имеет полость, соответствующую конфигурации будущего изделия.
Данный способ широко применяется для получения алюминиевых отливок, обладающих уникальными свойствами и использующихся во многих сферах: машиностроение, строительство, автомобилестроение, мебель (фурнитура, декоративные элементы) и др. Выбор технологии литья зависит от размеров, формы и требований к конечной продукции.
Литье в песчаные формы: доступный и простой метод
Литье в песчаные формы – самый распространенный и экономичный метод.
Процесс начинается с изготовления литейной модели, которую раньше делали из дерева, а сейчас – из пластика. Модель засыпается специальной смесью песка и связующего вещества, которая уплотняется прессованием. Затем расплавленный металл заливается в образовавшиеся полости через специальные отверстия. После охлаждения форму разбивают и извлекают отливку, которая требует дальнейшей обработки.
В современных технологиях используются вакуумные формы, заполняемые песком. Для изготовления формы применяют металлическую опоку, состоящую из двух бездонных коробов, которые засыпаются песком и утрамбовываются. На поверхности разъема снимается отпечаток модели, соответствующий форме отливки. Соединяя две формы, осуществляют заливку расплава.
Литье в кокиль: высокое качество и прочность
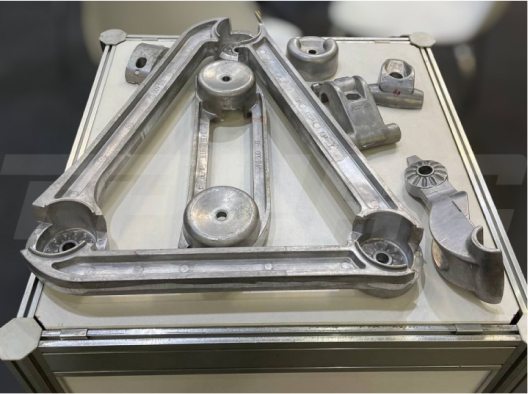
Это высококачественный метод, который подразумевает использование разборной металлической формы (кокиля). После застывания отливки кокиль очищается и используется снова.
Отличительной особенностью данного метода является то, что затвердевание жидкого металла происходит без внешнего воздействия. Полученные таким образом изделия обладают мелкозернистой структурой, обеспечивающей высокую прочность, герметичность и отличные механические свойства.
Кокиль используется для отливки из разных сплавов, в основном алюминиевых и магниевых, имеющих низкую температуру плавления. Один кокиль может использоваться до 1000 раз. Литье в кокиль очень эффективно для серийного производства, что является причиной его широкого применения для получения до 45% изделий.
Литье под давлением: эффективность и качество поверхности
Этот метод гарантирует высокое качество поверхности, которое не требует дополнительной обработки. Метод очень производителен и подходит для получения деталей различной формы, весом от нескольких грамм до десятков килограммов.
Литье под давлением позволяет получать сложные детали с криволинейными поверхностями, различными каналами и полостями. Применяется преимущественно для отливки из цинка, магния, латуни и алюминия.
Преимущества ЛПД:
-
Низкая стоимость.
-
Высокая точность размеров и формы отливки.
-
Возможность получения множества отливок из одной пресс-формы.
Недостатки ЛПД:
-
Длительность процесса.
-
Высокая стоимость изготовления пресс-форм.
-
Сложность получения отливок со скрытыми полостями.
-
Возможность образования газовых раковин и усадочных трещин.
Для изготовления алюминиевых отливок в ЛПД используют специальное оборудование с холодной горизонтальной камерой для прессовки материала, а также полуавтоматические машины для литья сплавов из цинка с горячей камерой прессовки и усилием запирания.
Литье по выплавляемым моделям: точность и сложность исполнения
Этот метод обеспечивает получение отливок высокой точности. Модель изготавливается из парафина, воска, стеарина или других легкоплавких материалов.
На модель наносится суспензия и производится обсыпка огнеупорным наполнителем, формируя оболочку, из которой затем выплавляется модель. Выплавка осуществляется в воде, под воздействием пара высокого давления или путем выжигания.
Следующий этап – прокаливание блока при температуре 1000 градусов Цельсия. Затем блок устанавливают в печь и в оболочку заливают расплавленный металл. Завершается процесс охлаждением отливки, ее выбивкой и отрезкой.
Преимущества данного метода:
-
Литье отливок из сплавов, которые трудно поддаются механической обработке.
-
Применение в серийном и единичном производстве.
Литье по газифицируемым моделям: экономичность и экологичность
Технология ЛГМ – это наиболее выгодное решение с точки зрения экономичности, экологичности и качества. Метод активно внедряется в мировом производстве, особенно популярен в США и Китае.
Модель изготавливается из пенопласта, помещается в песчаную форму, и таким образом получают отливки массой до 2 тонн и более, размерами от 40 до 1000 мм.
Метод активно применяется в двигателестроении для изготовления головок блоков цилиндров, отдельных блоков и деталей.
Преимущества ЛГМ:
-
Экономичность.
-
Экологичность.
-
Высокое качество отливок.
Центробежное литье: равномерное распределение металла
Центробежное литье применяется для получения деталей с формой тела вращения (гильзы, втулки) из чугуна, алюминия, стали и бронзы.
Расплав заливается в металлическую форму, вращающуюся со скоростью до 3000 об/мин. Центробежная сила равномерно распределяет расплав по форме, формируя отливку после кристаллизации.
Преимущества центробежного литья:
-
Высокая плотность и отличные механические свойства отливки.
-
Возможность формирования внутренних полостей без использования стержней.
-
Экономия сплава за счет отсутствия литниковой системы.
Литье в оболочковые формы: прочность и контроль качества
Литье в оболочковые формы позволяет получить точные фасонные отливки из металлических сплавов.
Оболочковая форма формируется из смеси песчаных зерен (кварцевых) и синтетического порошка, наносимой на нагретую металлическую модель. После образования слоя смеси ее избыток удаляется.
Преимущества метода:
-
Контроль над тепловым режимом охлаждения заготовок.
-
Возможность механизации процесса и повышения производительности.
Цветное литье: разнообразие сплавов и декоративных изделий
Цветное литье – это процедура изготовления отливок из цветных металлов (алюминий, бронза, латунь, медь).
Виды цветного литья:
-
Центробежное цветное литье (заполнение формы при ее вращении).
-
Литье в металлические формы с охлаждением (кокиль).
-
Литье в формы ПГС.
Преимущества центробежного цветного литья:
-
Высокое качество и экономичность.
-
Практически безотходный способ литья.
Цветное литье применяется в художественном литье для изготовления декоративных изделий, ворот, заборов, фонтанных конструкций и т. д. Сплавы цветного литья отличаются высокой прочностью и устойчивостью к коррозии.